- -- Precision Metal Welding System
- -- Resistance Welding Consumables & Accessories
- -- High Speed Automatic Cutting System
- -- Ultrasonic Plastic Welding System
- -- Automatic Welding System
Machine & Accessory
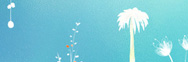
- Computerized Automatic Tab ..
- Herbert Resistance Welding ..
- Herbert Resistance Welding ..
- DANPS Nickel Plated Steel S..
- Electrode selection for res..
- Expert design and supply of..
- Selective Tin Plating Batte..
- Electrode selection for res..
- The Micro®-Weld CD 139 spot..
- Expert manufacturer in Sele..
News
Selection of Welding Electrodes
Date:2011-3-24 15:00:15 Hitnums:351
Welding electrodes are installed in the weld head. Their functions are to create pressure and to pass the maximum current with the minimum contact resistance.
The electrode must be matched to each application and must possess high electrical conductivity to transfer the current efficiently, high thermal conductivity to conduct the surface heat, and strength to withstand the dynamic compressive forces encountered during the weld cycle.
Parts made of highly conductive materials usually require electrodes of high resistance. Hard materials require soft copper-based electrodes. When welding dissimilar materials such as Copper and Nickel the normal choice would be a Molybdenum electrode against the Copper and a RWMA 2 or Copper & Aluminum oxide alloy electrode against the nickel.
The size of the weld will not be any larger than the electrode face. Therefore, it is important to use electrodes with identical face diameter for a desired weld nugget.
The current density at the welding interfaces varies as the square of the diameter of the electrode face. Electrodes should be dressed at regular period before they have worn to the point where they produce poor welds.
Electrodes should be dressed with 600 grit paper or polishing disk, not with a file.